We can detect imbalances of less than a nanometer
attocube systems AG has developed an interferometer, which can carry out contactless and high-resolution runout measurements in the sub-nanometer range. This permits imbalances equating to fractions of a nanometer to be accurately detected.
Minimal imbalance requires maximum competence
Everyone knows about imbalances in the wheels of a car. They lead to vibrations and greater wear in the vehicle. These runout errors can be remedied by balancing the wheels i.e. measuring the imbalance and applying a balancing weight. What may be simple on a car becomes a real challenge when bearing faults and imbalances need to be measured with sub-nanometer accuracy. This is the case in nano-physics, but also increasingly in industrial applications.
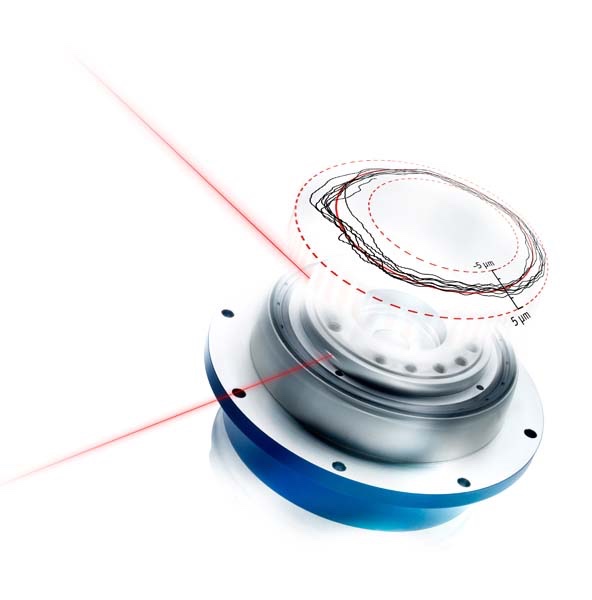
Precision in new dimensions
Great metrological precision is needed in anything relating to absolute rotational symmetry of drive spindles in CNC machine tools or motor shafts in servo drives, for example. attocube systems AG, a subsidiary of WITTENSTEIN, has developed an ultraprecise, contactless and working interferometer for measuring runout errors in fast rotating objects, a technology that sets standards.
Smart measurement
The IDS3010 is an optoelectronic linear measuring system with up to three optic heads. For example, to measure the runout of the shaft of a high-precision planetary gearbox, two sensor heads are aligned at a 90° angle to the rotating shaft. Each of these then scans the shaft by means of laser and continuously measures the distance to the shaft in fractions of a second.
Errors are quickly detected
The analysis by the interferometer allocates two linear distance values to each measurement – one for the 0°, and one for the 90° position. The deviation of these angle-related distances between measurements is a measure for the eccentricity of the shaft. The measurements are displayed as a circular curve which allows the position and severity of bearing faults and imbalances to be identified. This visualization and the electronic evaluation of the measurement data enables the user to draw conclusions as to the causes - ball-bearing fault or machine vibrations.
It's that simple
No specialist knowledge is required to operate the IDS3010: Because the compact optic heads have a large radiation angle, they can be positioned in hard to reach places with ease. Measurement can begin immediately after adjustment. A further benefit: The extremely small sensor heads only contain passive optic and mechanical components. This means that they can be used even in extreme industrial conditions such as heat, cold and vacuum.
The same applies to nanometer-precision measurements
The contactless and high-resolution runout measurement in the sub-nanometer range, combined with a high degree of integration and user-friendliness, opens up many possible applications for industry and laboratories: These start with the dynamic runout and lateral runout measurement, through the validation of distortion simulations to path-controlled setting of the bearing preload.